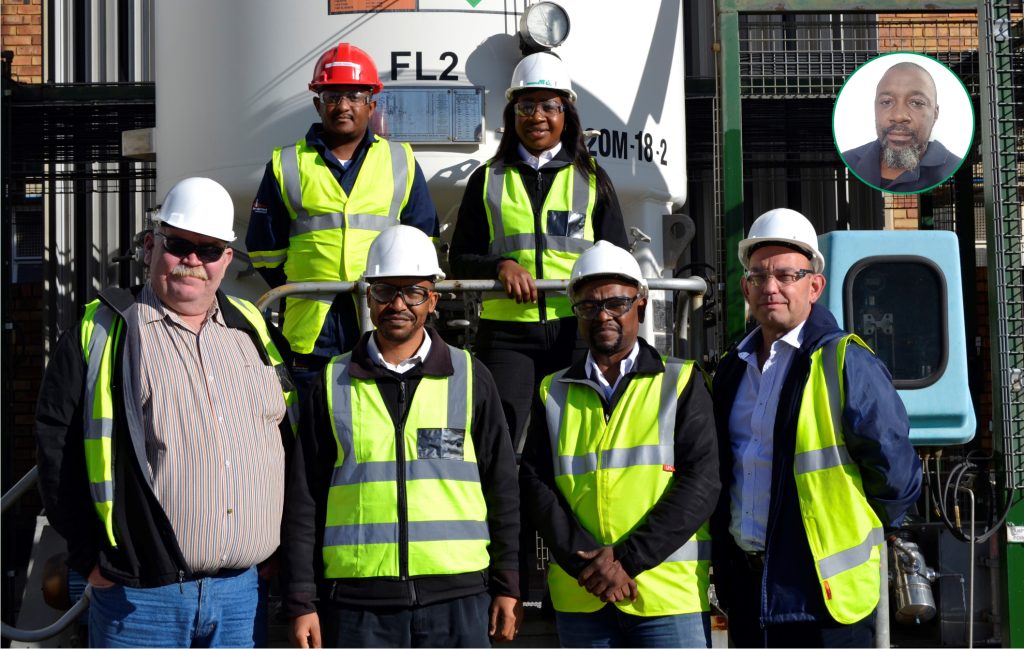
Back: Sivuyile Mdolo and Nana Phuti
Front: Phillip Venn, Vusi Ndebele, Elias Mpotu and Chris de Jager
(Thulani Nxumalo was also a key player in this project)
Air Products prides itself on its commitment to customer experience. This is reflected in the number of customers they have maintained long-standing relationships with. The solid foundation of these relationships stem from Air Products’ approach which uses; innovative measures and technology to provide customers with quality products that enable them to avoid delays and breakdowns in their operations. Air Products recently assisted their biggest argon customer, Columbus Stainless, to overcome a production challenge which could have had a severe impact on their operations.
The relationship dates back to the 1980’s, before the company was renamed Columbus Stainless. Over the years, Air Products has gradually increased the volume of industrial gas products to Columbus Stainless, the only stainless steel mill in Africa and part of the Acerinox Group of companies.
On 23 June 2022, the Air Products team was approached by Columbus Stainless to assist in providing a solution for the emergency oxygen supply. The Air Products team acted swiftly to ensure that Columbus Stainless could continue their production with a minimal downtime period averting delays for their export trade.
Finding a solution – combining industry knowledge, technical expertise and resources
Columbus Stainless was confronted with a major interruption in the oxygen supply via the pipeline. On the Friday evening, the General Manager for Supply Chain received an urgent call for assistance to provide a possible solution for the oxygen supply shortage.
Solutions and options were requested from key personnel within the company, which required late evening conversations and an after-hours site visit to discuss possible routes, viable options and equipment requirements which could be considered. These options were discussed and reviewed by both the Air Products Executives, Technical and Engineering teams early on the Saturday morning, and the below solution was presented to and accepted by the Columbus team later that afternoon.
Due to the oxygen supply pipeline interruption and the Air Products argon installation on site not being utilized, an option was recommended by the technical team to modify and utilize the existing argon storage and vaporization system for an alternate supply of oxygen into the plant. By changing the equipment service use from argon to oxygen, all required controls would be available with minor modifications. This would require the manufacture of a temporary pipeline to provide an interconnection between this installation and the plant oxygen supply pipeline.
The choice to modify the equipment service to oxygen was considered the safest and simplest solution, providing the best solution that could meet the customer’s target date expectations.
According to Nana Phuti, a leading female Senior Project Engineer at Air Products, having received the “green light” with the extremely ambitious timeline proposed, several contractors were activated, installation teams assembled, and preliminary requirements executed. She further explains that concurrently, material suppliers were contacted for required materials stock levels and availability.
With these preliminary actions having been fast tracked over the weekend, by Monday morning, an oversight and supervision team was assembled between the various departments, briefed and sent to site. These preliminary planning and activation activities assisted to significantly reduce timelines required to provide this solution to the customer.
The Air Products’ Technical, Bulk Engineering and Distribution departments team members involved, together with the contractor teams utilized, were able to modify the installation controls, convert the crude argon tank installation to oxygen service and install a temporary pipeline between the Air Products storage site and the identified connection point by the following Thursday.
Phuti further explains: “The process of converting the crude argon system to oxygen was seamless as Air Products uses oxygen clean components as a standard for all gas applications. The project team had to prepare the necessary safety assessments, project plans and costings in a concurrent process, whilst the contractors and technicians had to undergo the necessary inductions on site on Monday”.
As is the case with all installations, safety is a key priority as all the necessary procedures had to be followed, regardless of the time sensitivity of the project. The roles and responsibilities of the Air Products team members, contractors and Columbus Stainless teams were clearly defined for this project. The core requirement was to connect approximately 24 metres of three inch stainless steel pipe as a temporary gas supply solution.
Phuti explains what this four-day process entailed:
- The product in the tanks had to be run down, and the system had to be purged to change service from crude argon to oxygen.
- An oxygen fill flange with an adaptor had to be fabricated and installed onto the current crude argon fill flange.
- The crude argon low pressure (LP) tank control, electrics and transfer pump had to be isolated and disabled.
- Concurrently, a three inch stainless steel pipe had to be fabricated, welded and installed from the crude argon system to the tie-in point on site.
- The temporary pipeline still had to pass the standard quality requirements, and all the welds passed the key NDT (non-destructive testing) requirement of 100% x-ray.
- Modification of tank calibration volume set points, tanks selection and indication for temporary oxygen application had to completed, as well as modifying the delivery and fill procedure to incorporate the temporary oxygen supply requirement.
- The team worked on a shift basis around the clock to complete the temporary installation piping and to also assist third party oxygen suppliers to deliver oxygen to the converted storage tanks.
- Air Products worked together with the incumbent oxygen supplier and the Columbus Stainless team to plan for the commissioning into oxygen service and decommission out of oxygen service of this modified supply system.
Good planning and a team effort leads to a solidly welded solution
“A project of this nature not only requires swift action, but also familiarity with the product characteristics, safety and design requirements, and ensuring effective and constant communication between all the parties. Furthermore, the project team had to ensure that key role players are familiar with their responsibilities according to the project plan and that they execute their tasks within the project timeframe. It is equally important to update the customer and manage their expectations in terms of the completion of the project,” says Phuti.
“The project was quite advanced in the sense that they had to connect the pipe to an existing oxygen supply source. We are fortunate to collaborate with contractors and a technical team who are experienced and prepared to do whatever was necessary to assist the customer to continue with their production”, said Phuti.
“Each person in the team was committed to do their bit to enable the client, Columbus Stainless to overcome this challenge”.
Columbus Stainless Engineering Manager, Alec Russell, remarked that the interruption to the production is a huge problem, and the downtime costs are something that every company dreads. Fortunately, with the commitment from Air Products, we were able to resolve the problem within a few days. It is in times like these that we experience the value of a longstanding relationship with a supplier that will go beyond what is required to assist in a time of crisis, he said.”